Introduction
Rapid prototyping and traditional prototyping are two widely used methods in the product development process. Both approaches have their own set of advantages and disadvantages. In this article, we will explore the pros and cons of each method to help you make an informed decision when choosing the right prototyping technique for your project.
Rapid Prototyping
Rapid prototyping, also known as 3D printing or additive manufacturing, is a modern approach that allows for quick and cost-effective production of prototypes. The process involves creating a three-dimensional object by adding layers of material one on top of another.
Pros of Rapid Prototyping
1. Speed and Efficiency
One of the biggest advantages of rapid prototyping is its speed. With this method, you can quickly produce prototypes, allowing for faster iterations and design improvements. This can significantly reduce the overall development time and time-to-market for your product.
2. Cost Savings
Rapid prototyping eliminates the need for expensive tooling and molds required in traditional prototyping methods. This can lead to significant cost savings, especially for small-scale production or when multiple iterations are required.
3. Design Flexibility
With rapid prototyping, you can easily make design modifications and adjustments during the prototyping phase. This flexibility allows for more creative exploration and ensures the final product meets the desired specifications.
4. Complex Geometries
Rapid prototyping enables the creation of intricate and complex geometries that would be challenging or impossible to achieve with traditional methods. This allows for greater design freedom and opens up possibilities for innovative product features.
Cons of Rapid Prototyping
1. Material Limitations
Although rapid prototyping offers a wide range of materials to choose from, the choices may be limited compared to traditional prototyping methods. This can pose a challenge if your product requires specific material properties or if you plan to test the prototype under extreme conditions.
2. Surface Finish
Rapid prototyping may not always provide the same level of surface finish as traditional prototyping methods. Depending on the chosen technology and material, the prototypes may have visible layer lines or rough surfaces. This can affect the aesthetics of the product and may require additional post-processing.
Traditional Prototyping
Traditional prototyping refers to the conventional methods of creating physical prototypes, such as machining or molding. These methods have been used for decades and offer their own set of benefits and drawbacks.
Pros of Traditional Prototyping
1. Material Variety
Traditional prototyping methods offer a wide range of materials to choose from, including metals, plastics, and composites. This allows for more accurate representation of the final product’s material properties and behavior.
2. Surface Finish
Traditional prototyping methods often result in superior surface finish compared to rapid prototyping techniques. This is especially important if your product requires a high-quality appearance or if you plan to use the prototype for marketing or display purposes.
3. Testing Validity
Traditional prototyping methods can provide a more realistic representation of the product’s performance and functionality during testing. This is particularly beneficial for products that need to undergo rigorous testing or simulations before entering production.
Cons of Traditional Prototyping
1. Time-consuming
Traditional prototyping methods typically involve longer lead times
Summary:
Rapid prototyping, also known as 3D printing or additive manufacturing, has revolutionized the way prototypes are created. Unlike traditional prototyping methods that involve time-consuming and costly processes such as machining or molding, rapid prototyping enables quick and cost-effective production of physical models. This approach allows designers to iterate rapidly, make modifications on the go, and significantly reduce development time.
On the other hand, traditional prototyping methods like CNC machining or injection molding still hold their ground as viable options in certain scenarios. These methods offer high precision and can be ideal for producing complex or large-scale prototypes. However, they often require specialized skills, expensive equipment, and longer lead times.
Both rapid prototyping and traditional prototyping have their merits and drawbacks, and the choice between the two depends on various factors including project requirements, budget, timeline, and desired level of fidelity. By understanding the pros and cons of each ap blog here proach, designers and engineers can make informed decisions when selecting the most suitable prototyping method for their specific needs.
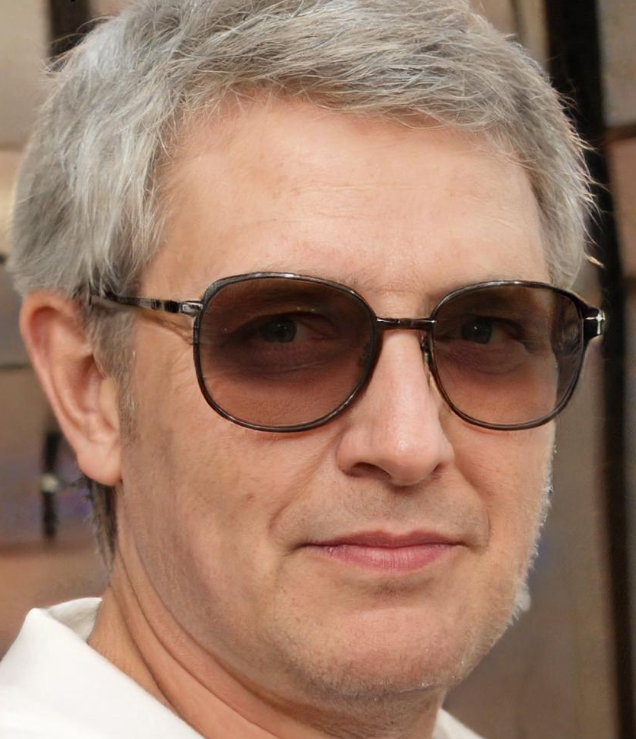