Introduction
Offset printing is a widely used printing technique in which the inked image is transferred from a plate to a rubber blanket and then onto the printing surface. It is known for its high-quality results and ability to handle large print volumes. However, like any printing process, offset printing can encounter various issues that affect print quality. In this article, we will explore common print quality issues in offset printing and provide troubleshooting tips to fix them.
1. Poor Ink Coverage
In some cases, you may notice areas on the printed material where the ink coverage is inconsistent or insufficient. This can result in a patchy appearance or faint prints. To resolve this issue:
- Ensure the ink is properly mixed and has the correct viscosity.
- Check for any clogged or damaged ink rollers and replace them if necessary.
- Adjust the ink keys on the press to achieve the desired ink density.
2. Blurred or Smudged Prints
Blurred or smudged prints can occur due to several reasons, including:
- Excessive fountain solution on the plate, leading to ink emulsification. Reduce the amount of fountain solution used.
- Worn-out or damaged blankets. Replace them to ensure proper ink transfer.
- Incorrect pressure settings between the plate and blanket or blanket and paper. Adjust the pressure to achieve optimal contact.
3. Ghosting
Ghosting refers to the faint reproduction of an image or text that appears in unintended areas. This issue can be caused by:
- Dirty or damaged blankets or rollers. Clean or replace them to eliminate ghosting.
- Insufficient drying time. Ensure proper drying of the printed material before stacking or handling.
4. Uneven Ink Density
Uneven ink density can result in variations in color intensity or patchiness. To improve ink density consistency:
- Check the ink fountain roller settings and adjust them to ensure even ink distribution.
- Inspect the plate for any damage or wear that may affect ink transfer.
- Verify the ink/water balance and make necessary adjustments.
5. Paper Jams
Paper jams can disrupt the printing process and damage the printed material. To prevent paper jams:
- Ensure the paper is properly aligned and free from any tears or wrinkles.
- Regularly clean and maintain the paper feed system to prevent accumulation of dust or debris.
- Check the paper thickness and compatibility with the press specifications.
6. Registration Issues
Poor registration refers to misalignment of colors, text, or images on the printed material. This can be caused by:
- Improper plate mounting. Ensure accurate plate positioning and secure mounting.
- Inconsistent blanket tension. Adjust the blanket tension to achieve precise registration.
- Mechanical issues with the press. Regularly service and maintain the press to prevent registration problems.
7. Dot Gain
Dot gain is the increase in dot size during the printing process, leading to a loss of detail and color accuracy. To minimize dot gain:
- Use a
Summary
In this blog post, we will delve into various print quality issues that can occur during the offset printing process. We will discuss problems such as blurred or fuzzy prints, banding, color inconsistencies, and improper ink drying. For each issue, we will explain the possible causes and provide step-by-step solutions to rectify them. Additionally, we will offer tips on preventive maintenance and calibration to ensure consistent print quality and minimize the occurrence of future problems. By the end of this guide, you will have a comprehensive understanding of how to troubleshoot a look here nd fix common print quality issues in offset printing, enabling you to achieve outstanding results with your printing projects. Let’s get started!
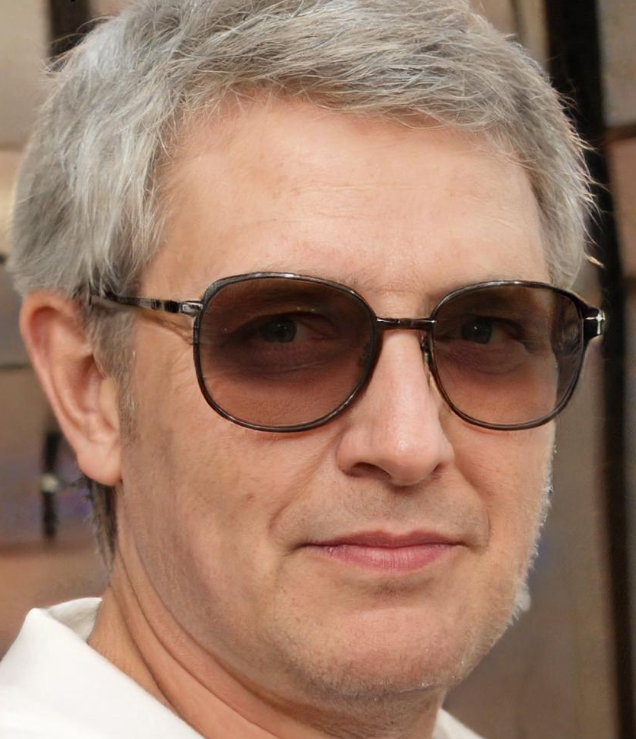